IACMI (the composites institute) member, Local Motors, is applying the advantages of additive manufacturing to the large-scale needs of automotive manufacturing. Transforming an industry that has historically relied on mass production techniques, its work is matching the pace of technology discovery and responding to quickly changing customer needs for transportation and other mobility devices for a new generation, all while dramatically reducing production time and costs.
The Need
Manufacturing of vehicles can be customized to meet many of the needs of today’s buyers. Customers are seeking enhanced functionality for specific needs along with lower costs and faster delivery times. These challenging demands are being met by Local Motors with microfactories in Knoxville, Tennessee, D.C. and Arizona.
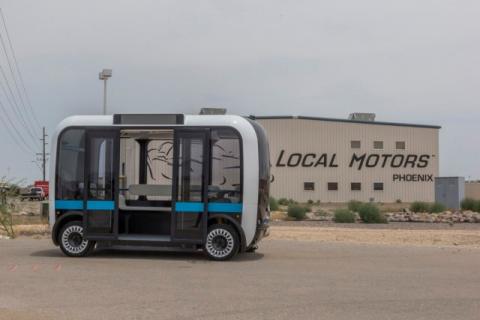
A Solution in Progress
Local Motors is changing how vehicles are manufactured and sold in their microfactories through its use of a revolutionary large-scale 3D printer and other advanced vehicle technologies. The innovation started with Olli 2.0, its self-driving, electric, eight-person shuttle bus. Olli’s parts are 3D printed, assembled, and shipped within one week.
The process begins with the company’s materials-testing technology and direct digital manufacturing software. Vehicles are designed and tested for problems, and solutions are developed using the software and small 3D models from desktop printers rather than through larger prototypes. This offers customization options without the need for large capital investments to retool a factory line, while lessening waste and utilizing recyclable and recycled materials.
After the models are thoroughly tested and reviewed, the company puts the world’s largest 3D printer to work to build the vehicle. The printer is the Thermwood LSAM, built specifically for producing large-scale structures and parts using composite materials via an additive approach.
The process enables Local Motors to create customized vehicles, including parts made and adapted all in-house in a fraction of the time required for traditional manufacturing processes.
Partners
IACMI brought together partners for a technical research and development project led by Local Motors, including the University of Tennessee and Oak Ridge National Laboratory. They also leveraged the 3D printer from Thermwood Manufacturing Corporatin in Dale, Indiana. The companies explored a process that would lower material costs, lessen environmental impact, and increase domestic production capacity.
Results to Date, Projections for the Future
Local Motors has realized a significant reduction in design-to-manufacturing cycle time, and cut the production time itself from four weeks to only one week using the digital additive process. Developing, testing, and producing their products in-house have led them to be heralded as the world’s first digital OEM.
The company’s additive technologies and flexible micro-factory configuration is enabling a concept-to-final customized product timeline of less than one year, which is inviting a variety of industries and customers to consider the infinite possibilities for new large-scale mobility and transportation devices. In addition, the products can be easily upgraded to keep up with changing customer preferences and needs.
Potential industries who can optimize advanced manufacturing capabilities such as these include infrastructure, defense, housing, and more.
“Local Motors’ goal is to change the way vehicles are manufactured and sold. Small batches of locally produced vehicles allow us to customize vehicles to best suit the needs of a specific market and make transportation smarter, safer, and more enjoyable.”
- Jacqueline Keidel, company spokesperson
The U.S. Department of Energy helped established IACMI in 2015.