The ARM (robotics institute) technology Project “Automated Defect Inspection for Complex Metallic Parts” has yielded impressive results, including detection rates above 95%, a speed of approximately one minute per part, and an expected 345% return on investment if deployed at one site. GKN Aerospace is adopting the technology, and has already built the developed inspection cell in a factory.
Beyond current limits of human inspection, a reliable robotic inspector enables inspection of complex metallic parts at all times of day with no loss in consistency, reduces impacts of human decision fatigue, and will slash manufacturing costs by reducing part escapes. The team’s central innovation is that fusing noncontact imaging data – robotically collected at the right positions and in the right environment – enables high-quality, consistent surface profiling at required operation speeds. From there, machine-learning based data analytics continuously improves inspection performance using accumulated data.
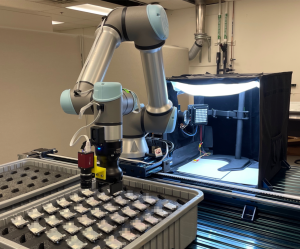
The first step to such ground-breaking automation is creating the inspection environment to the standards of the most experienced inspectors. The team developed a controlled imaging environment that blocks light contamination to enable accurate and consistent collection of surface profiles. Lens filtering then controls reflections and minimizes glares from the complex part geometry. By respecting fundamental principles of light and reflection, the team then created robotic data collection that reveals not only area defects such as corrosion, but also sub-millimeter machining lines and dents.
Curved geometry disrupts focus and lighting – small defects demand high-resolution macro images. The team’s robotic inspection system automatically partitions and images the part section by section. A procedure then extracts only the useful, in-focus areas.