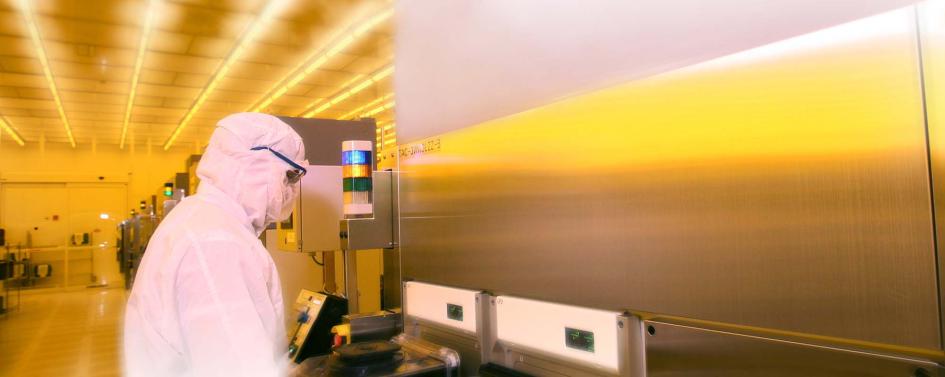
The growth in electronic devices, smart machines and connectivity throughout the world means almost every industry is dependent upon semiconductors. A global shortage of microelectronic semiconductor chips, made worse with changing demands and supply chain issues, has disrupted U.S. automobile manufacturers and is expected to impact consumer electronics, medical devices and networking equipment.
Semiconductors — the tiny chips that enable modern technologies — are critical to America’s economy, job creation, technology leadership and national security. There are chip fabs in 18 states, and semiconductors are the fifth-largest U.S. export. But the U.S. share of global semiconductor manufacturing has fallen from 37 percent in 1990 to 12 percent. In its recent assessment of the semiconductor supply chain, the Biden Administration has advocated for expanding federal investment in the semiconductor manufacturing ecosystem. The CHIPS for America Act as passed by the Senate includes $52 billion in federal investments for domestic semiconductor research, design, and manufacturing provisions.
The institutes in the Manufacturing USA network are working to accelerate commercialization of faster, more flexible and more efficient semiconductors in the U.S. They are doing so with integrated photonics, flexible hybrid electronics, and wide bandgap power electronics. This work in next-generation chips is critical for anchoring a semiconductor supply chain in the U.S. and ensuring small- and medium-sized manufacturers remain the foundation of a strong economy and secure nation.
Manufacturing USA® is a network of 16 manufacturing innovation institutes and their sponsoring federal agencies — the Departments of Commerce, Defense and Energy. It was created in 2014 with advanced manufacturing technologies in mind, and its mission is to secure U.S. global leadership in advanced manufacturing by connecting people, ideas, and technology.
Emerging Technologies Are Transforming Semiconductors
The semiconductor industry and its high-precision work involve long lead times and high manufacturing costs. A cutting edge silicon fab can take five years to build and cost more than $20 billion. Several new foundries are under construction but are not expected to be online until 2023 or later.
It’s also essential to invest in future technology. Since nothing travels faster than the speed of light, photonic circuits create opportunities for faster data transmission, lower power consumption devices, and increased bandwidth. Likewise, traditional printed circuit boards are rigid, and that rigidity creates limitations, which is why flexible hybrid electronics are in such high demand for applications such as medical wearables, apparel, and other uses. Silicon chips also have limits in their power capabilities; while silicon carbide and gallium nitride power electronics provide substantial performance improvements in high-power applications.
The U.S. is a global leader in each of these three emerging technologies. Investing in building fabs and the supporting ecosystems for these technologies will be crucial for the future supply chain for semiconductors. There are about 250 manufacturers in the U.S. in the integrated circuit board ecosystem that could work on these new technologies, boost the value of their products and benefit from the U.S. leadership in these areas. Countless additional companies will incorporate these technologies into their products to unlock new capabilities.
Integrated Photonics – the Intersection of Light and Electronics
Integrated photonics, or photonic integrated circuits (PICs), are similar to their electronic counterparts but use light to make digital signals instead of electrons. By moving data with photons (light) rather than electrons, many of the energy, heating, and processing bottlenecks are alleviated that stem from the use of electronics and copper wires. AIM Photonics’ advanced manufacture of silicon photonics can integrate key photonic devices: modulators, lasers, detectors, and waveguides, along with state of the art electronics. In essence, integrated photonics is merging light with electronics.
AIM Photonics, a member of the Manufacturing USA network, operates its photonics prototyping services through the Albany Nanotech Complex in Albany, N.Y. The Albany Nanotech complex is the most advanced publicly owned 300mm wafer R&D facility in the world. AIM has developed a silicon photonics Multi Project Wafer (MPW) to shorten design time, improve manufacturing efficiency, and lower price of entry for companies that want to develop new silicon photonics applications. AIM has also built a photonics and electronics test, assembly and packaging facility in Rochester, N.Y., completing the capability to build a product from initial concept and design through packaging and product prototypes.
Today, integrated photonic chips, often referred to as silicon photonics, are primarily found in transceivers, which are a critical part of data centers. Photonics, however, has many applications. Silicon photonics can be seen in an inexpensive, disposable bioassay application in which a sensor is able to read whether a drop of blood has COVID-19. Silicon photonics also could expand the use of LiDAR (light detection and ranging) instead of radar (radio detection and ranging). LiDAR uses lasers with a much shorter wavelength than radar, which results in higher levels of accuracy and precision. LiDAR allows smaller objects to be detected in more detail. Silicon photonics chips will be in many more applications and may become the future scaling vector of microelectronics.
Creating Flexibility for Circuit Boards Opens Up Many Applications
Legacy printed circuit boards are limited by their rigidity, which means as electronic devices have gotten smaller, it has been a technical challenge to create novel system form factors for both commercial and military applications.
NextFlex, America’s Flexible Hybrid Electronics, has developed low-cost printed circuits that allow the use of semiconductors in small flexible systems. These systems deliver the “Internet of Things” connectivity that can conform to surfaces and bodies in wearable and flexible devices.
NextFlex has a state-of-the-art Technology Hub that has successfully proven a robust manufacturing process by producing multiple functional samples of a flexible Arduino®-compatible microcontroller, an open-source electronics platform based on easy-to-use hardware and software. That process uses 60 percent fewer steps, resulting in faster manufacturing at lower cost and an end-product that is smaller, two-thirds lighter, and usable in more applications than a rigid board.
This will allow the semiconductor industry to expand beyond centralized and expensive processing units. Flexible hybrid electronics take advantage of circuit boards that cost less and use less power. These flexible circuit boards are being built into a wide range of products used in health and performance monitoring, structural monitoring for buildings and bridges, soft robotics and antennas.
Industrial Operations Also Benefit From More Efficient Semiconductors
In addition to speed and flexibility, the future of semiconductors also depends on devices that can operate at higher temperatures, frequencies and voltages than current state-of-the-art electronics. This is the focus of PowerAmerica, which has worked with its industry partners to advance the manufacturing and implementation of silicon carbide (SiC) and gallium nitride (GaN) wide bandgap semiconductors.
Compared to traditional silicon, SiC and GaN power electronics operate more efficiently, can withstand higher temperatures, have a smaller footprint, and can reduce overall system cost. But SiC semiconductor devices are more expensive to produce.
PowerAmerica worked with X-FAB to create a power semiconductor foundry in Lubbock, Texas. The facility can fabricate SiC power devices with economies of scale approaching those of silicon-power devices. A number of PowerAmerica members are utilizing X-FAB capabilities as fabless semiconductor companies or using X-FAB capacity to complement their internal manufacturing efforts.
The institute also supports the GaN power electronics ecosystem and the commercial applications that can benefit from this efficient technology. For example, PowerAmerica partners have used SiC and GaN technologies to greatly improve Electrical Vehicle charging capabilities while lowering costs and barriers.
PowerAmerica has completed its funding stream from DOE and continues its program supported by its 67 members from the power electronics ecosystem.
Innovation is Driving A New Domestic Supply Chain for Semiconductors
The Manufacturing USA network supports the development of new technologies necessary to revamp the U.S. supply chain in microelectronics. .
In 2020, the 16 institutes collectively worked with over 2,000 member organizations to collaborate on more than 500 major research and development projects and engaged over 70,000 people in building workforce knowledge and skills in advanced manufacturing. State, industry and federal funds contributed $400 million to these activities.
To learn more about how integrated photonics, flexible hybrid electronics and wide bandgap technologies are accelerating the commercialization of faster, more flexible and more efficient semiconductors, visit the Manufacturing USA institutes’ page.