Sustainability is a core focus across all 17 Manufacturing USA institutes, especially the seven institutes sponsored by the Department of Energy. Transitioning industry to clean energy is projected to reduce carbon emissions by 55 percent, a critical step toward achieving the U.S. goal of net-zero emissions by 2050. However, the remaining 45 percent will require a fundamental shift in how we design, build, and consume products and materials. Here are two examples of how institutes are going beyond the transition to clean energy to more holistically address sustainability.
Preserving a Critical Mineral Through Innovative Aluminum Recycling
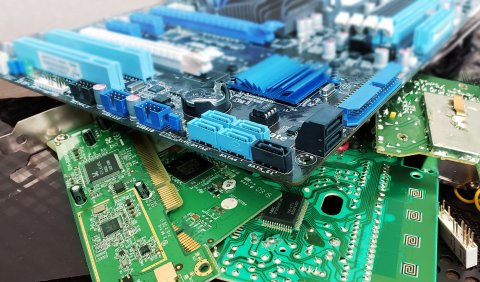
The REMADE Institute is championing a "Re-X" approach – reusing, remanufacturing, recovering, and recycling materials – to promote a circular economy. This holistic strategy not only reduces waste but also drives innovation in sustainable manufacturing. In a circular economy, materials are not discarded after they are used but are brought back into the economy through a variety of means. REMADE’s projects range from design – in which 80 percent of a product’s life cycle costs and environmental footprint is determined upfront – to reducing waste generation in the manufacturing process and making it easier to extract materials for reuse. One of REMADE’s success stories involves utilizing smart sensors and artificial intelligence to optimize the sorting of scrap metal to be able to reuse aluminum. Recycling aluminum saves up to 95 percent of the energy needed to make it from scratch and preserves one of the nation's most critical minerals.
Learn more about REMADE
Pioneering Portable, Eco-Friendly Electronics
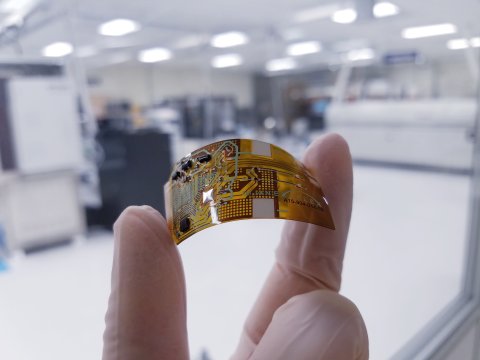
NextFlex, the Flexible Hybrid Electronics Institute, designs and builds electronics with additive processes and novel materials. The flexible designs lead to lighter weight, unique form factors, and fewer manufacturing steps, which improve performance while reducing manufacturing costs. Another advantage is reducing the impact of electronic system manufacturing on the environment. Multiple studies estimate that flexible hybrid electronics can reduce water, power, and waste streams by more than 10 times. NextFlex and its members are working on aqueous-friendly inks that conduct electricity, which can reduce or eliminate the need for wires, and are using biodegradable substrates such as paper and other recyclable materials. This new type of electronics has applications in medical devices, wearables, aerospace, automotive, and more.
Learn more about NextFlex